Troubleshooting
These are the most common issues that an user might encounter during the beamtime. If the issue is not present here, please pen down in the eloggy so that we have updated information to deal with the specific issue effectively. You may also consult the floor coordinator to help you.
There is no beam!
Was there a beamdump? First make sure there is current in the ring http://status.maxiv.lu.se/
Is the frontend closed? Make sure the Veritas frontend is open. The text behind Veritas on the statuswebpage will be green if the frontend is open
Is anything blocking the beam? In the synoptic, follow the path of the beam make sure that the valves are green.
Light at the slit? We have a camera at the monochromator exit slit, a viewer can be launched from the synoptic, click “Start…” on the top right of the viewer to get an image. If you can see beam here, then you know you have light through the mono.
Fault in RIXS Client
This is how the RIXS gui will look like when it is at fault. If you get this fault, you need to restart RIXS server.
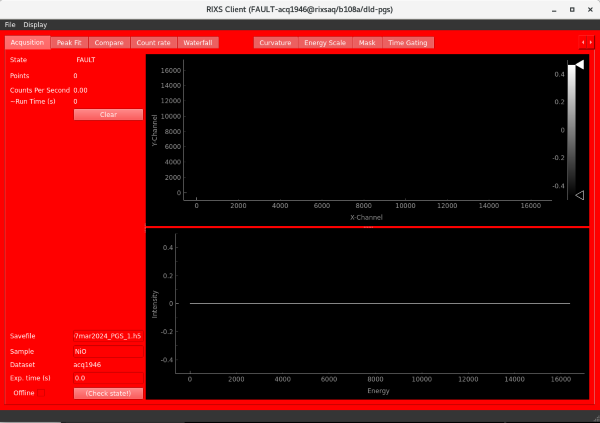
RIXS Client at fault state
What should you do to restart RIXS server ?
open ‘terminal’
type and enter ‘astor’ (servers repository)
Under ‘Veritas servers’, double click ‘b-316a:a101630-ctl-dcu-01 (Rixsaq Arm computer)’
right click ‘Rixsaq/b316a’ and select ‘Restart server’
Here is the pictorial representation:
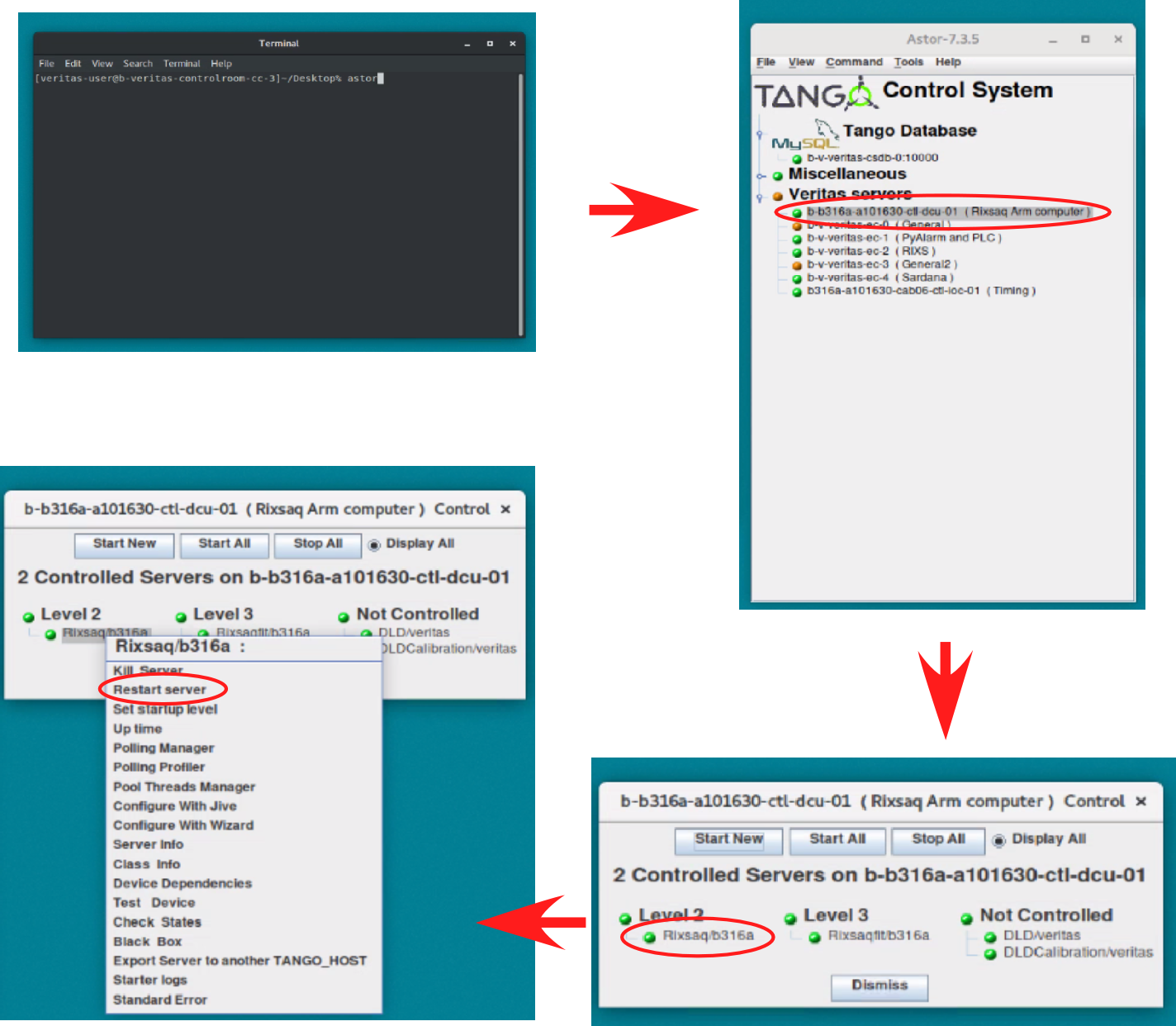
How to restart RIXS server
Manipulator Motor axis is not moving at all
First, please check it is not physically hit something. Generaly, this should not be the case unless the hardware limit switch is hit.
If the hardware limit switch is nit hit, yet the motor not moving then try esync it. In terminal, run ‘spock’. run ‘ipap_esync’ followed by the name of axis: a_mp1_x, a_mp1_y, a_mp1_z, a_mp1_yaw. Eg.: to esync ‘a_mp1_x’ axis, run ‘ipap_esync a_mp1_x’
If the motor is still not moving, reset icepap by enable/disable “pysical” switch. hold toggle to disable until LED indicator change (around 2sec). Hold toggle switch to enable side for around 4 sec. and if status LED indicator becomes green it is recoved. This was reqired once for a_mp1_y axis which has brake on it.
If the problem persists, reach out to the floor coordinator or the local contact.
Note: this axis is not connected to PLC, so emergency stop for q-angle does’t stop this axis.